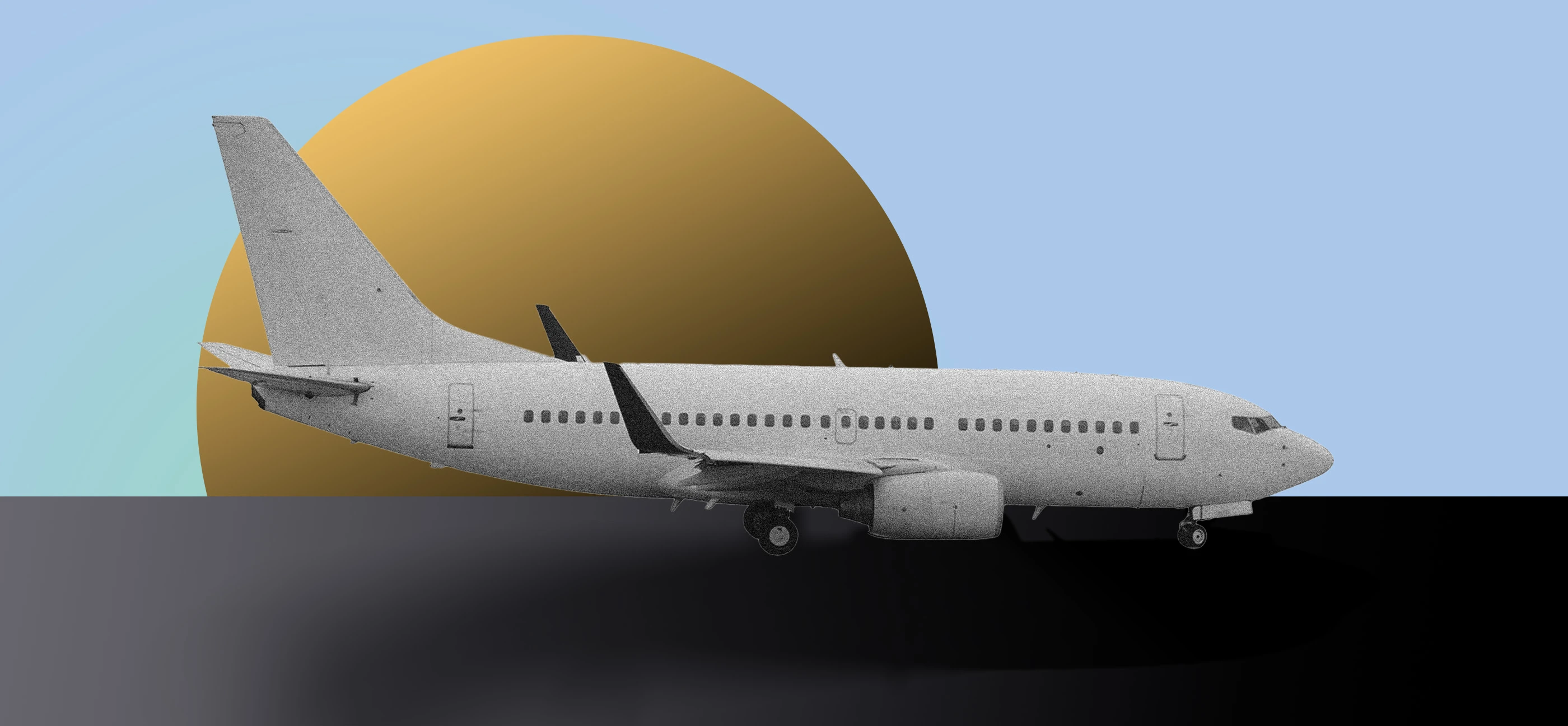
Once again, Boeing’s 737 MAX is back in the headlines.
After two crashes that killed 346 people in 2018 and 2019 and five years of ensuing design changes and regulatory scrutiny, the 737 MAX is grounded again after a mid-air blowout of a fuselage panel on January 5. After loose bolts were discovered on other MAX 9s, the Federal Aviation Administration (FAA) grounded the planes and opened an investigation into whether MAX is safe to fly, accompanied by a stern warning, saying, “This incident should have never happened, and it cannot happen again.”
Boeing has also experienced repeated problems in design and production with its newest jumbo jet, the 787 Dreamliner. Such frequent, repeated crises point to a deeper issue than isolated engineering mishaps. The underlying cause of these issues is a leadership failure that has allowed cultural drift away from Boeing’s once-vaunted engineering quality.
William Boeing created the commercial aviation industry. For the next century, Boeing was the leading producer, based on its excellence in aircraft design and safety. Boeing’s problems today date back to former CEO Philip Condit, who made two ill-fated decisions that dramatically changed Boeing’s culture. The first was acquiring archrival McDonnell Douglas in 1997, a leader in military aviation with its fighter jets and Boeing’s major competitor in commercial aviation. In contrast to Boeing’s culture of engineering excellence, McDonnell Douglas focused on cost-cutting and upgrading older airplane models at the expense of all-new aircraft.
Secondly, in 2001 Condit moved Boeing’s headquarters from its original home in Seattle to Chicago—all to gain $60 million in state and local tax credits over 20 years. With none of its businesses based in Chicago, the move separated Boeing’s corporate executives from its engineering and product decisions and alienated its Seattle-based engineers.
Leader turnover, ethical lapses, and buybacks
After Condit resigned in 2003 following an ethics scandal, Boeing’s board convinced former McDonnell Douglas executive Harry Stonecipher to come out of retirement to replace Condit. Stonecipher, a General Electric (GE) alum, immediately set out to change Boeing’s culture, proclaiming, “When people say I changed the culture of Boeing, that was the intent, so that it is run like a business rather than a great engineering firm.”
One of Stonecipher’s fated decisions was to turn down the proposal from Boeing’s head of commercial aviation to design an all-new single-aisle aircraft to replace the Boeing 727 (FAA-certified in 1964), 737 (1968 certification) and 757 (1972). Instead of designing a new airplane incorporating all the advances in aviation technology from the past 30-40 years, Stonecipher elected to maximize profits from older models and use the cash to buy back Boeing stock.
Just two years after taking over, Stonecipher resigned after violating the company’s code of conduct. Rather than promoting the internal candidate, Alan Mulally, who headed up commercial aviation and led the development of the highly successful Boeing 777, the board recruited ex-GE executive Jim McNerney to succeed Stonecipher. At the time, McNerney was CEO of 3M, a tenure that lasted just four years. Meanwhile, Mulally became CEO of Ford, where he led one of the most important business turnarounds in history.
Maximizing earnings, but at what cost?
By 2011, Boeing found its 737 losing out to rival Airbus’s A320neo with major customers like American Airlines. Rather than designing a new aircraft to replace the 737, McNerney opted for a five-year program to upgrade to the 737 MAX. This decision required the redesign to stay within FAA’s original type-certification with the same flying characteristics. Boeing also agreed with customers like Southwest Airlines to avoid retraining pilots and upgrading its training manuals. These decisions minimized short-term cost to maximize short-term earnings.
In my experience with advanced technology products, quick fixes often lead to design compromises that create more problems. This happened with the 737 MAX in 2015 when it encountered stall problems. Rather than further design changes that would have risked the 737’s original type-certification, Boeing opted for a major software change that was not disclosed to the FAA or described in its pilot’s manual.
The flaws in the software design that took flight control away from the pilots without their knowledge based on data from a single sensor, ultimately led to the two 737 MAX crashes in 2018 and 2019, causing the deaths of 346 people. After the first crash, Boeing issued a statement that offered pilots and passengers “our assurance that the 737 MAX is as safe as any airplane that has ever flown the skies.” That assurance came back to haunt Boeing four months later when the second MAX crashed.
When Boeing leadership failed to ground its fleet of 737 MAX planes, the FAA forced them to do so, pushing Boeing into a lengthy set of regulatory inspections, tests, and design changes lasting 20 months. During that time, its customers waited for aircraft they desperately needed in service. Then Congress held a damaging hearing that eventually forced Boeing’s board to relieve then-CEO Dennis Muilenburg. Today, ex-GE executive David Calhoun, a Boeing board member since 2009, has the onerous task of restoring Boeing’s business and its quality standards.
The cost of reputational damage
When we discuss the Boeing cases in my classes at Harvard Business School, I ask participants, “Are Boeing’s problems caused by individual leadership failures or a flawed culture?” The answer “both” eventually emerges. It was the actions of Condit and Stonecipher that turned Boeing’s culture from excellence in aviation design, quality, and safety into emphasizing short-term profit and distributing cash to shareholders via stock buybacks.
McNerney compounded the problem through his decision to launch a quick fix to the 737 rather than design a new airplane. Muilenburg was left with the flawed aircraft, but failed to ground the planes after the first crash and pinpoint the root cause of the failure. The Boeing board, which is composed of exceptional individuals, failed to preserve Boeing’s culture and reputation.
Ironically, decisions made in the name of shareholder value over the past two decades have cost its investors $87 billion since 2018. The long-term damage to Boeing’s reputation and market position is even greater as Airbus has outsold Boeing in new aircraft orders each of the last five years.
Now CEO Calhoun faces immediate pressure to fix the MAX fuselage panel and win back market share. However, his real task must be to restore Boeing’s culture of aviation excellence—a long-term project that is the only real solution to restore this once iconic company to aviation leadership.
Bill George is an Executive Fellow at Harvard Business School, and former Chair and Chief Executive Officer of Medtronic. He doesn't hold a financial stake in Boeing, its competitors, or any airlines.
You Might Also Like:
Feedback or ideas to share? Email the Working Knowledge team at hbswk@hbs.edu.
Image note: Illustration was created with artwork from AdobeStock/John Vlahidis.