Does Lean Improve Labor Standards? Management and Social Performance in the Nike Supply Chain
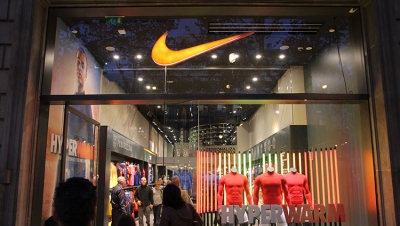
Key Insights for Managers
While many firms seek to buy only from suppliers whose working conditions meet the firm’s labor standards, little is known about how firms can encourage their suppliers to improve their working conditions. This study by Greg Distelhorst, Jens Hainmueller, and Richard Locke examines the effects of Nike encouraging some of its apparel suppliers to adopt lean manufacturing, a systematic approach to minimizing all forms of waste including defects, overproduction, waiting, and motion. Lean manufacturing requires more worker training and often results in workers gaining more responsibility. Intended to help improve suppliers’ operational efficiency, this study found that adopting lean also led to improvements in their working conditions in ways that improved adherence to Nike’s labor standards. The factors most driving this improvement include greater accuracy in tracking work hours and paying wages, greater adherence to the requirements allowing workers to take one day off per week and to provide legally mandated benefits, and fewer instances of work hours exceeding maximum thresholds.
The study found no evidence that adopting lean led suppliers to improve their adherence to Nike’s health, safety, and environmental standards. Lean management’s effects on labor standards differed country: suppliers in India, Thailand, Malaysia, and Vietnam exhibited noticeable improvements, but suppliers in China did not. The study’s results were based on regression analysis of over 1,800 Nike audits conducted during 2009-2013 of 300 factories, with as many as 21% adopting lean in any given year. The factories were located in 11 countries.